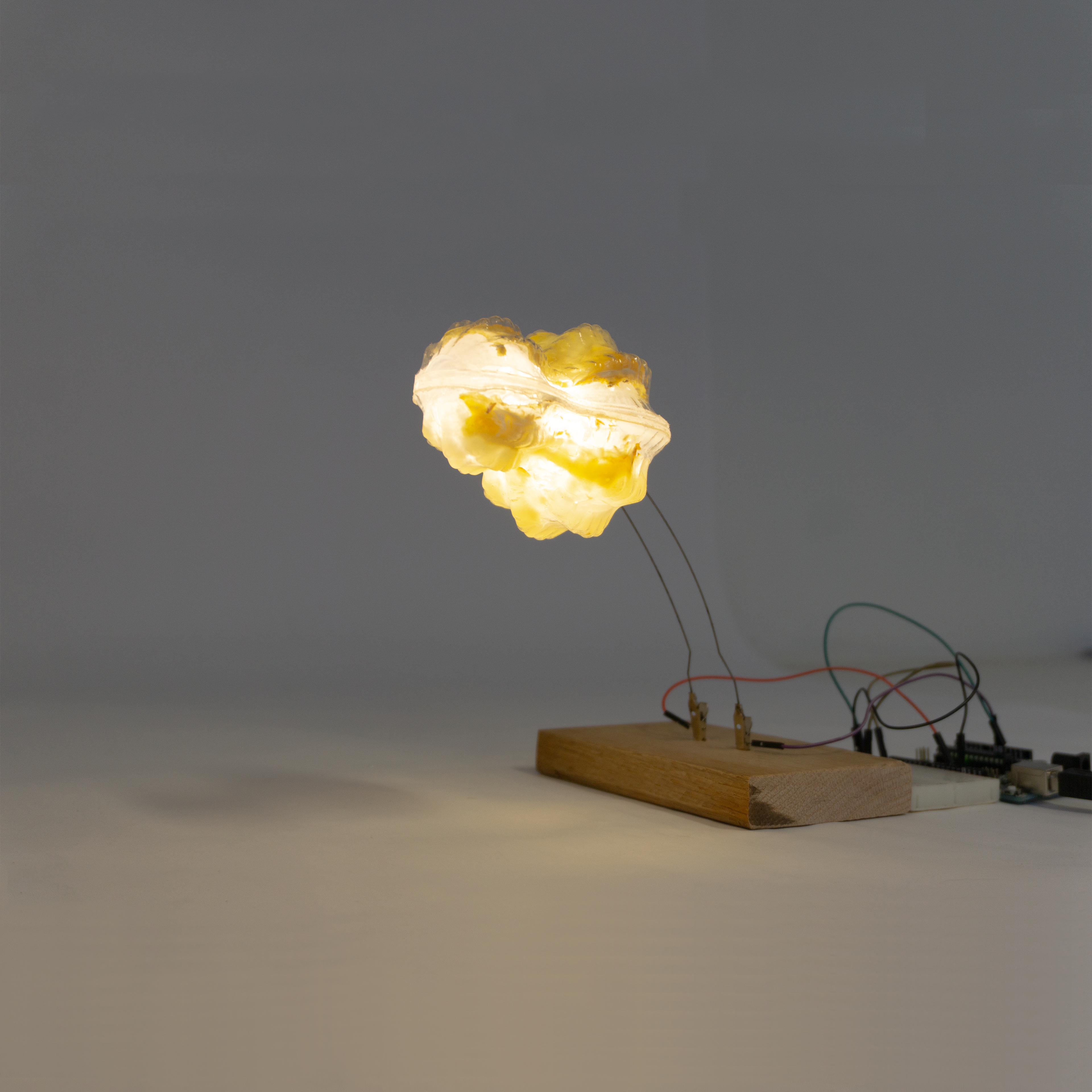
The project emphasizes the feathered, fuzzy texture created by mycelium and explores how a thin layer of mycelium can diffuse light.
Mold Design
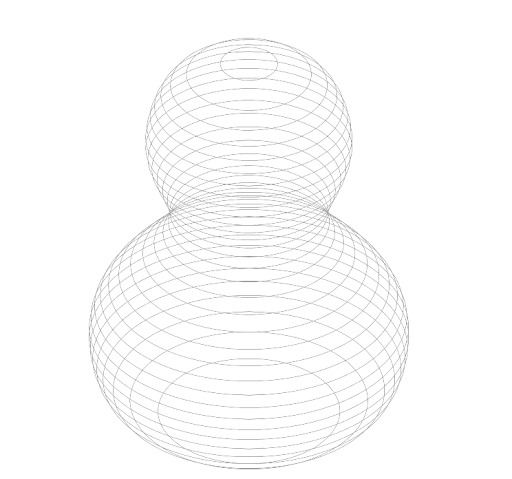
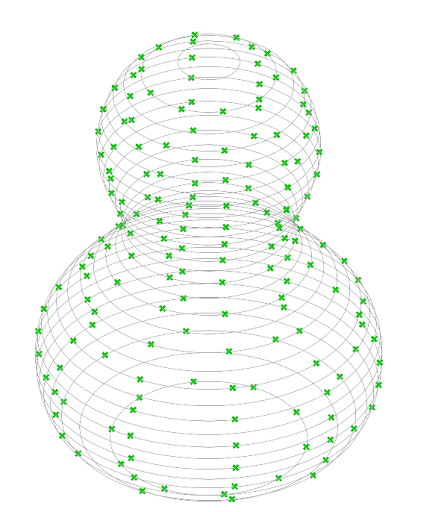
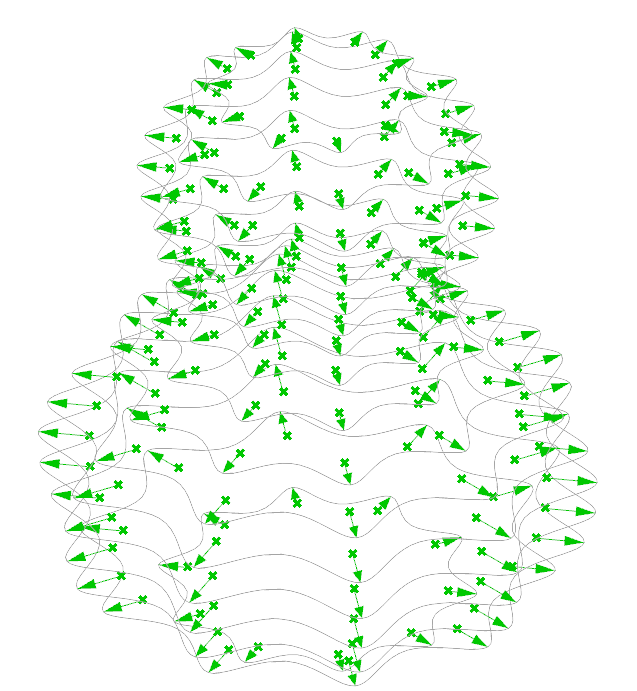
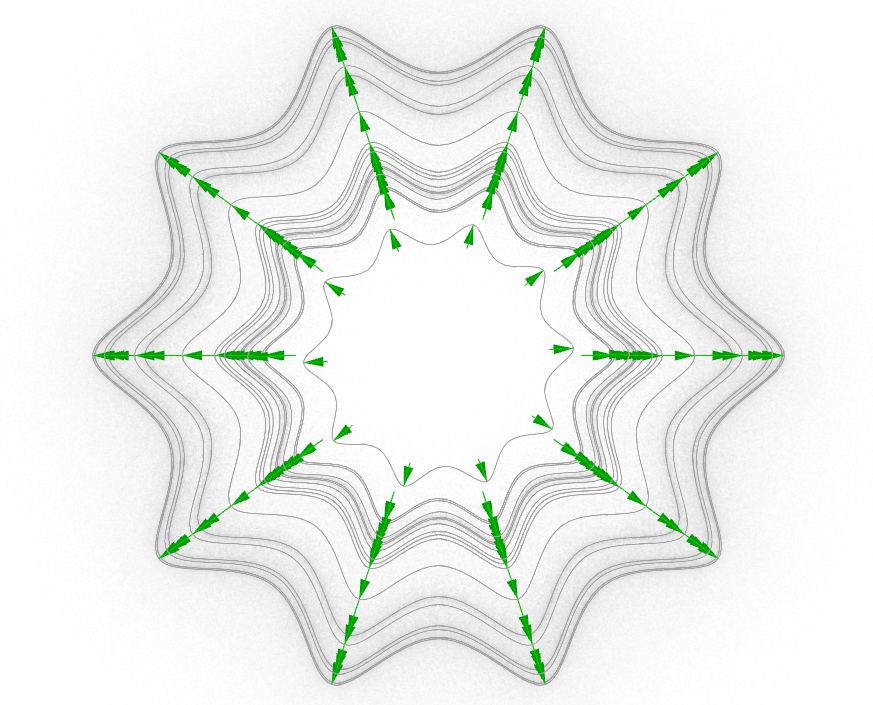
The geometry starts with a continuous 1/16'' (0.063'')-thick gap and transitions through an extrusion to a 0.035''-thick gap. The thicker section provides enough material for the mycelium to establish, while the thinner area encourages the formation of a delicate, feather-like layer with strong light-transmitting qualities.
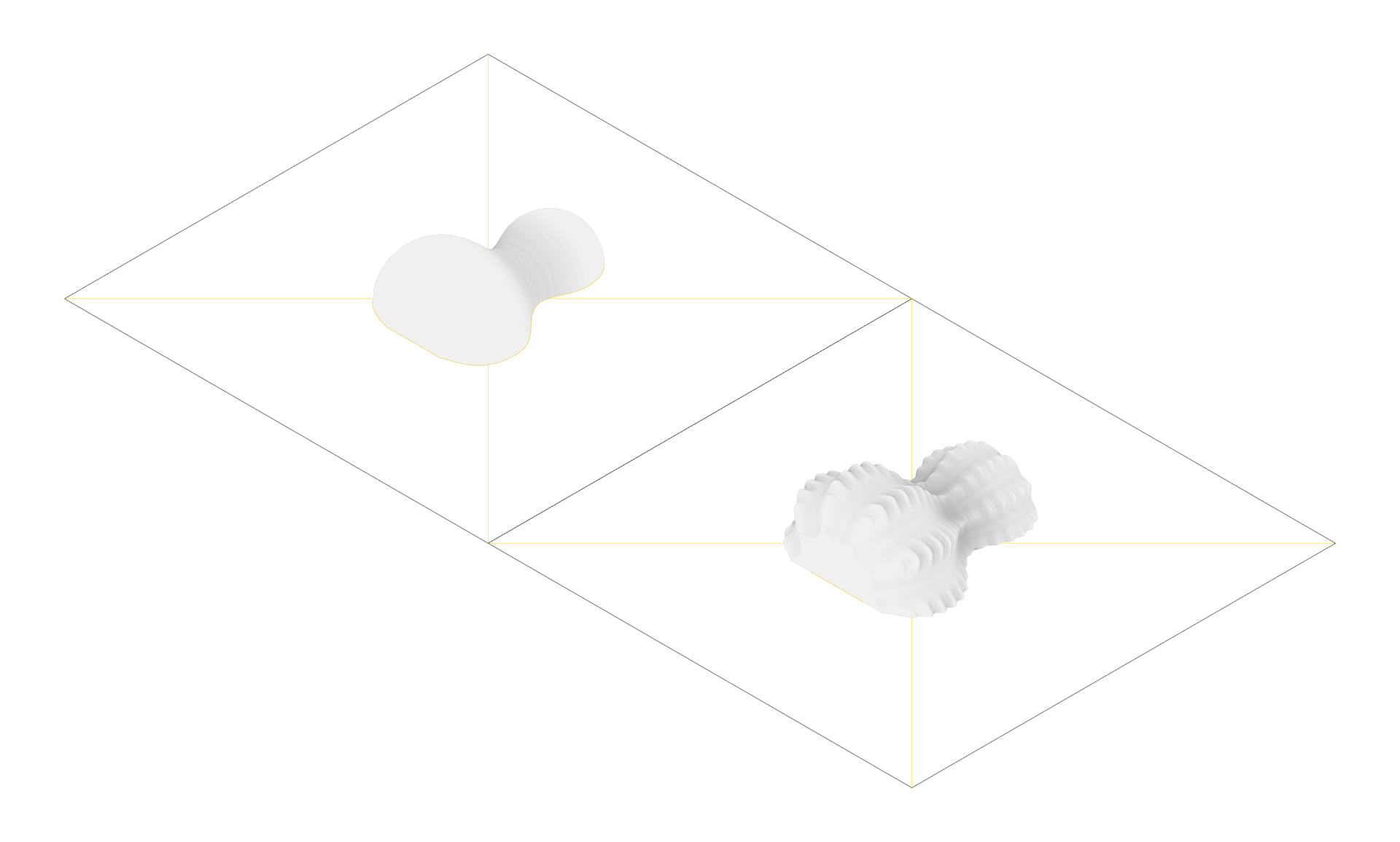
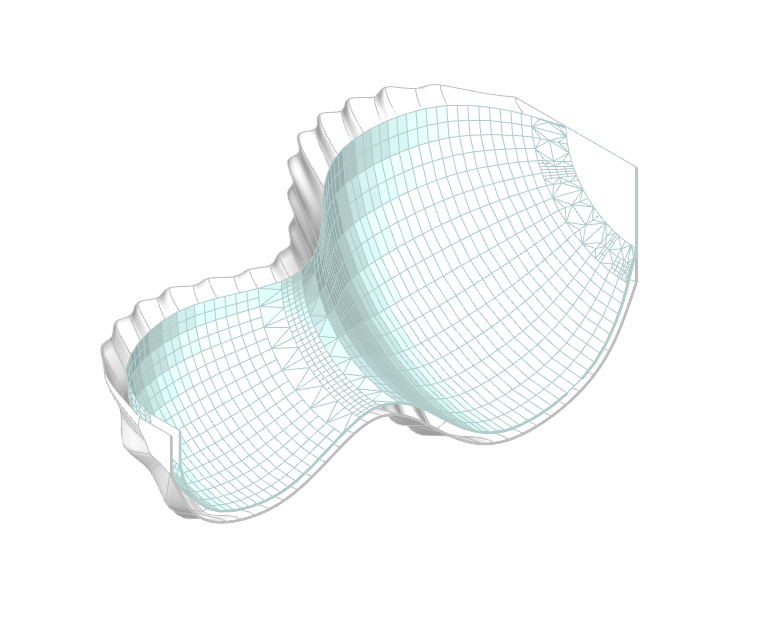
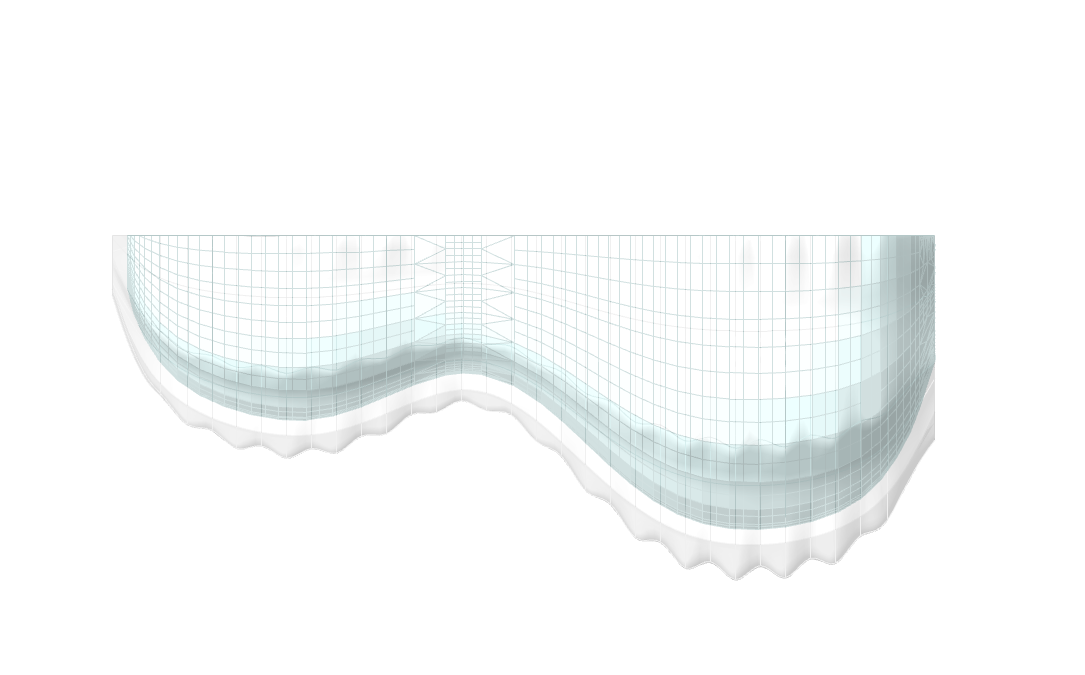
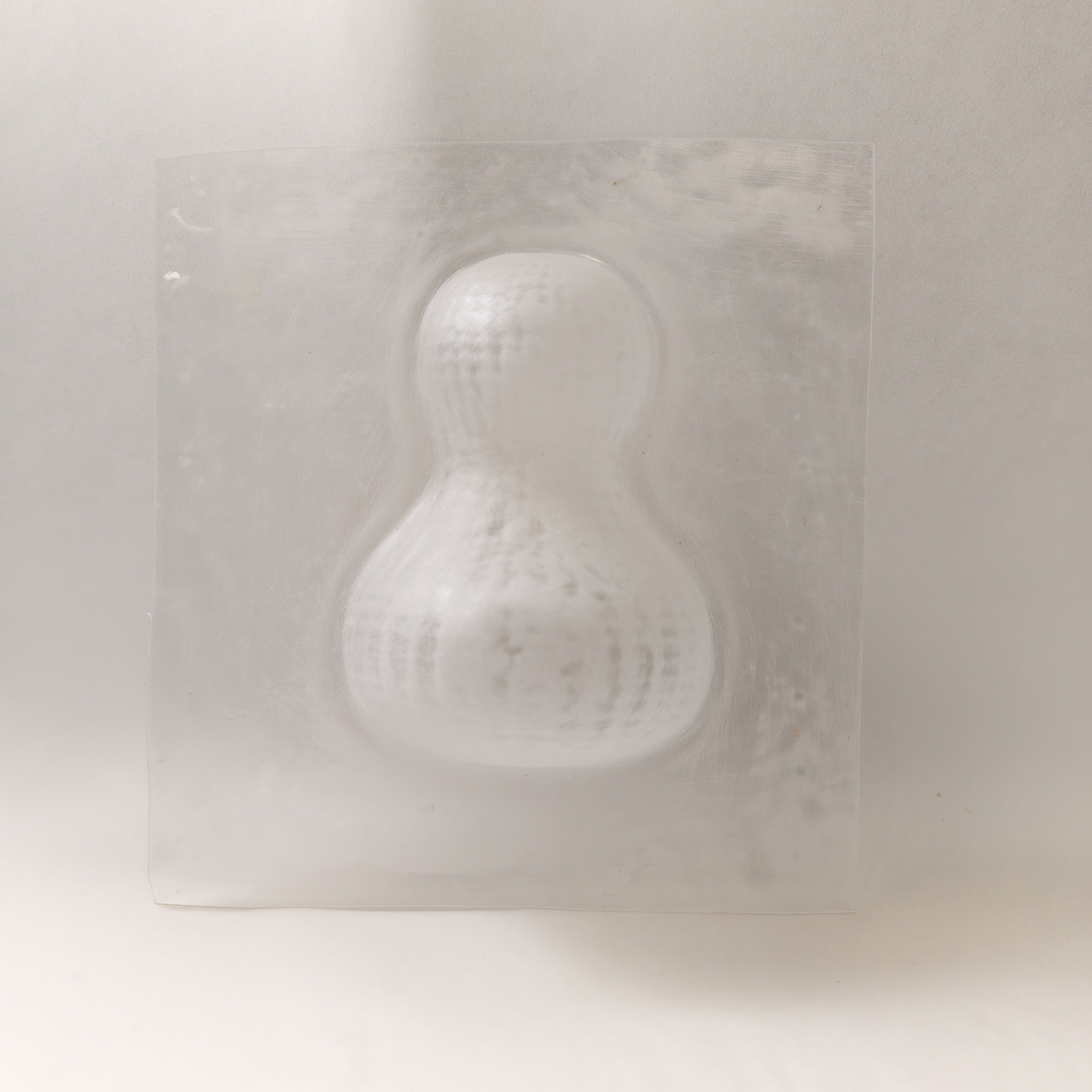
Half of the geometry is 3D printed, while using vacuum form PETG to quickly create few sets of mold. Hot liquid agar is poured into the molds and left to cure overnight. Once cured, the inner mold (with the smooth surface) is removed, while the exterior mold remains in place to prevent the agar from deforming. The agar is then placed on top of a grain sponge where mycelium has already been established, allowing it to quickly colonize the agar surface.
Substrate_Agar
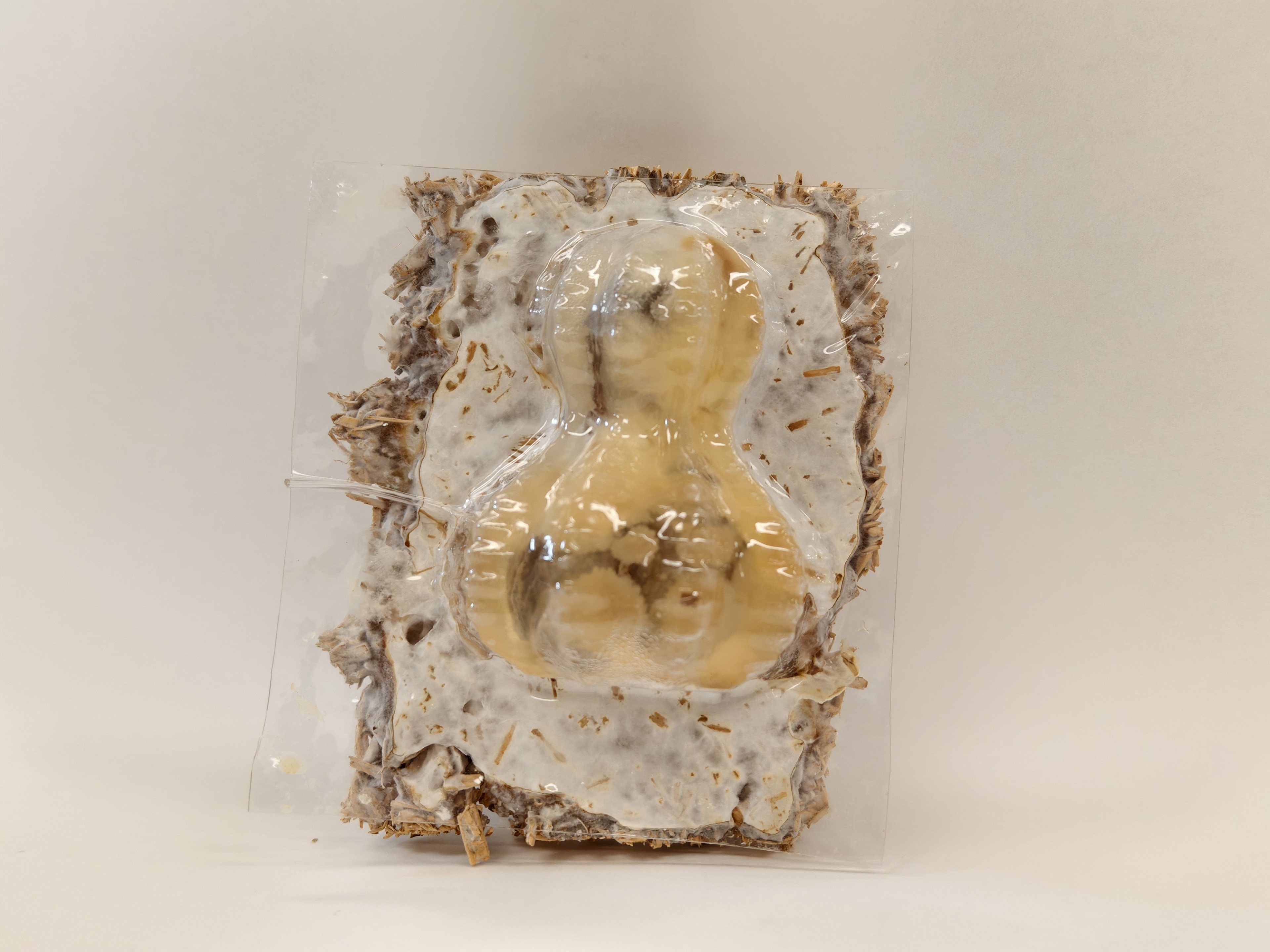
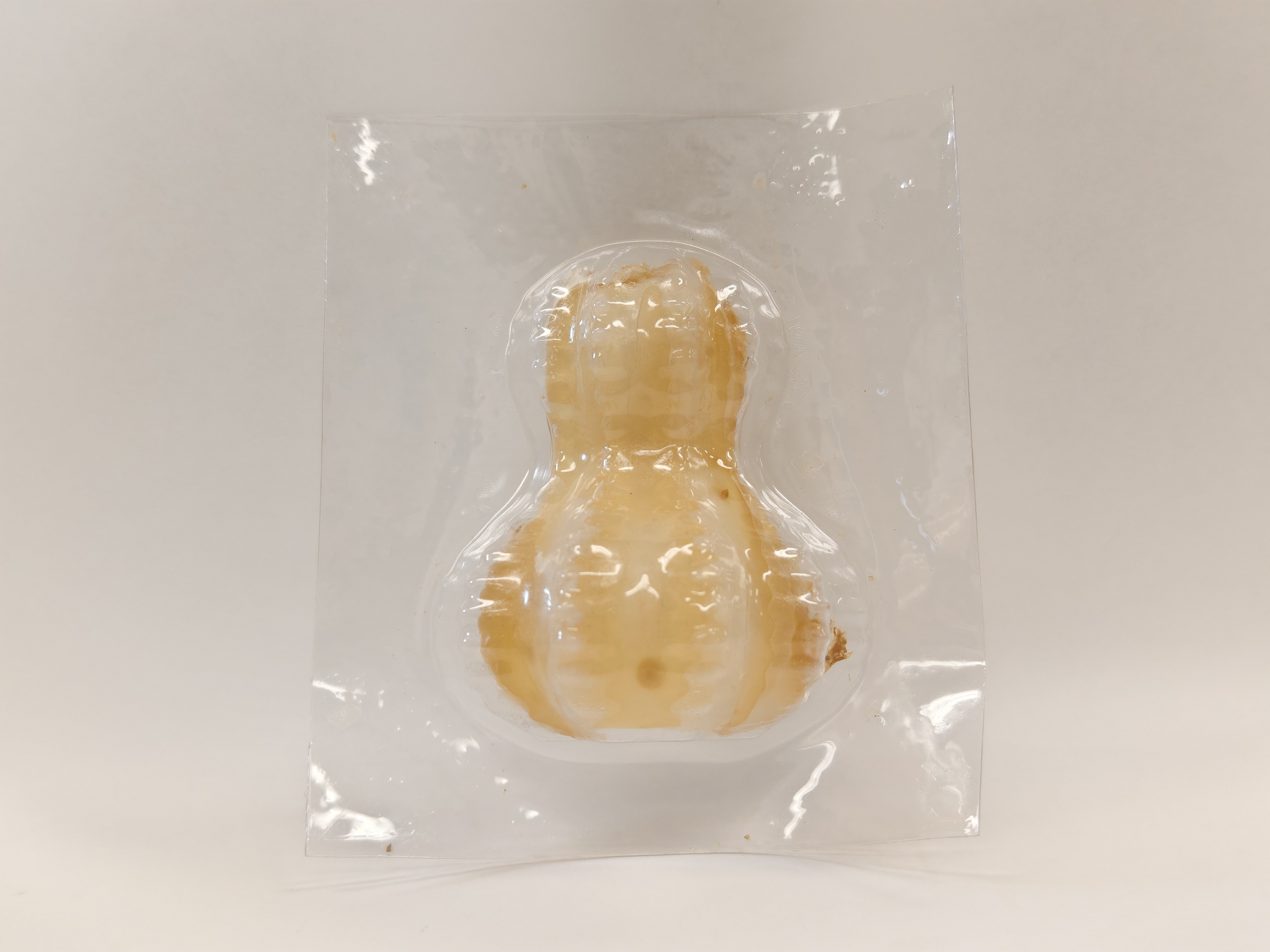
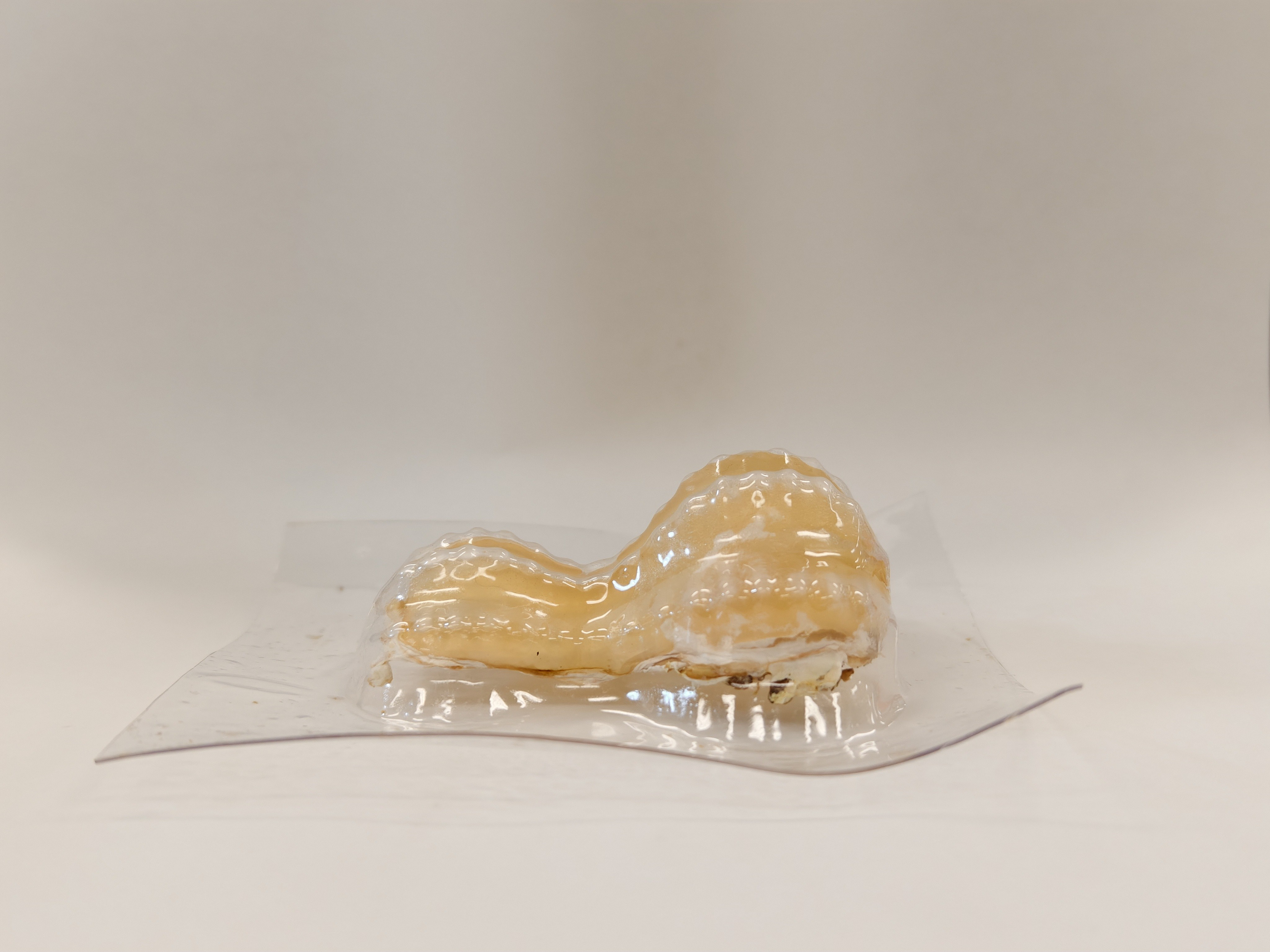
The performance of mycelium based material is highly dependent on the chosen substrate. Agar was selected for its excellent light-transmitting properties.
Growing Process
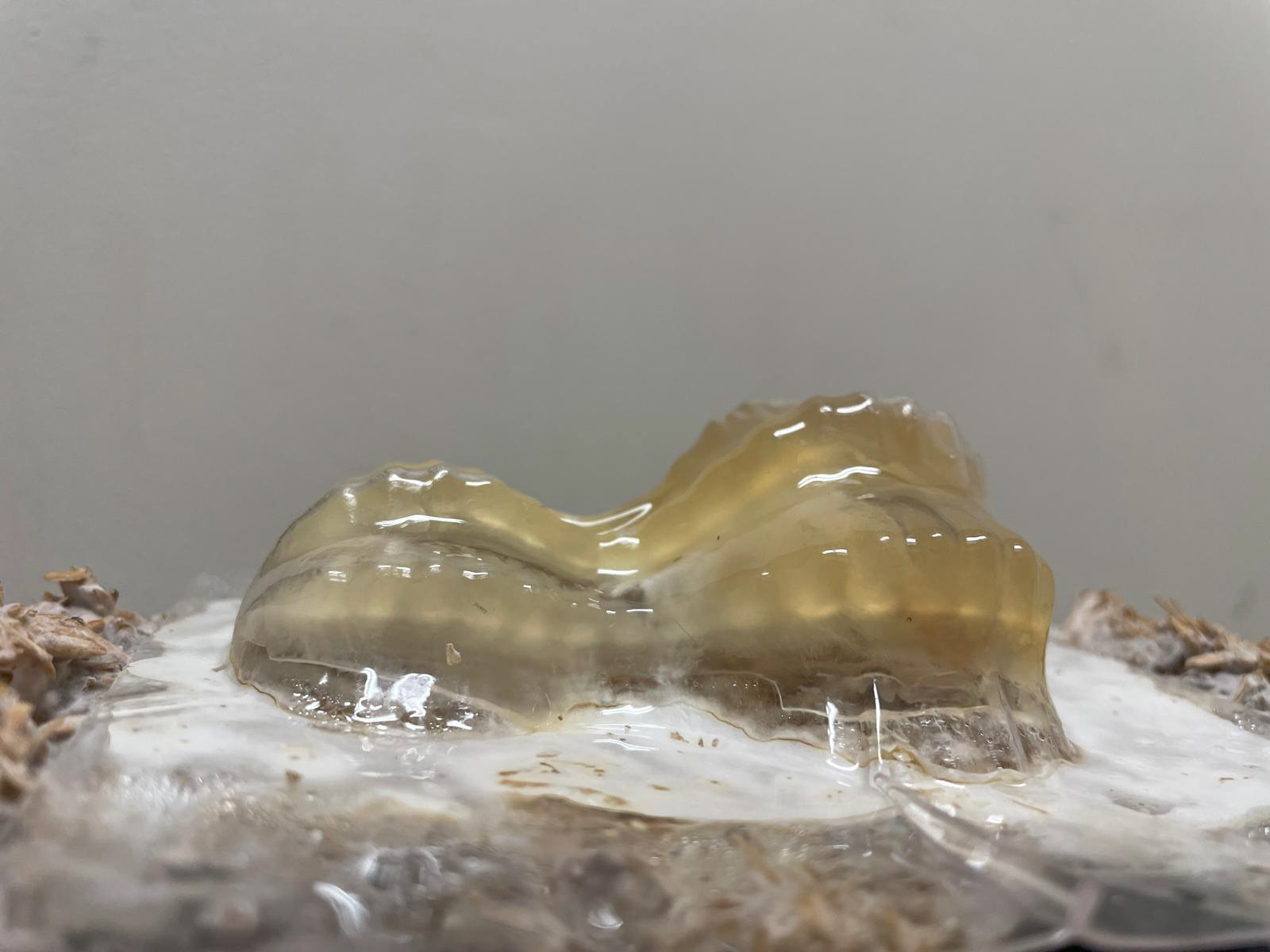
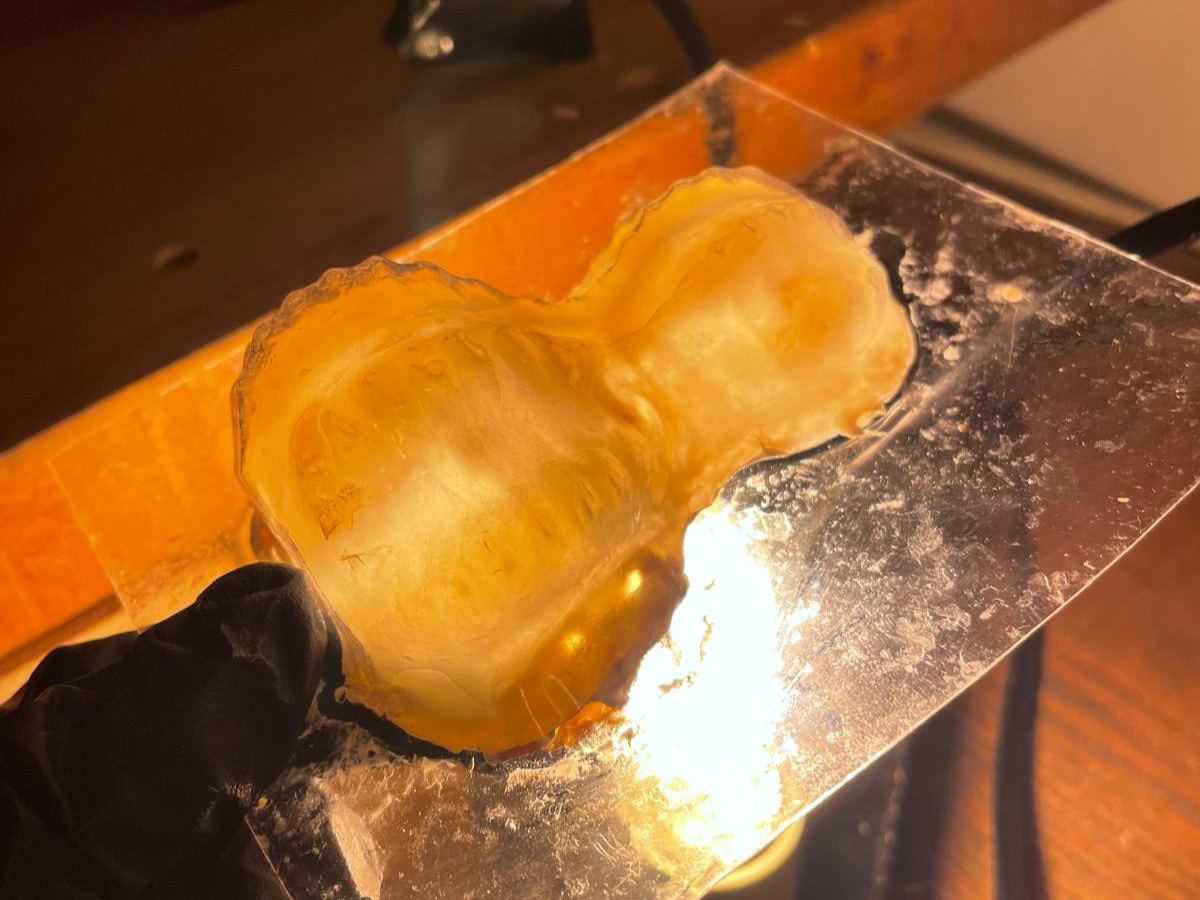
Denser and thicker mycelium growth is concentrated around the fin area.
Light
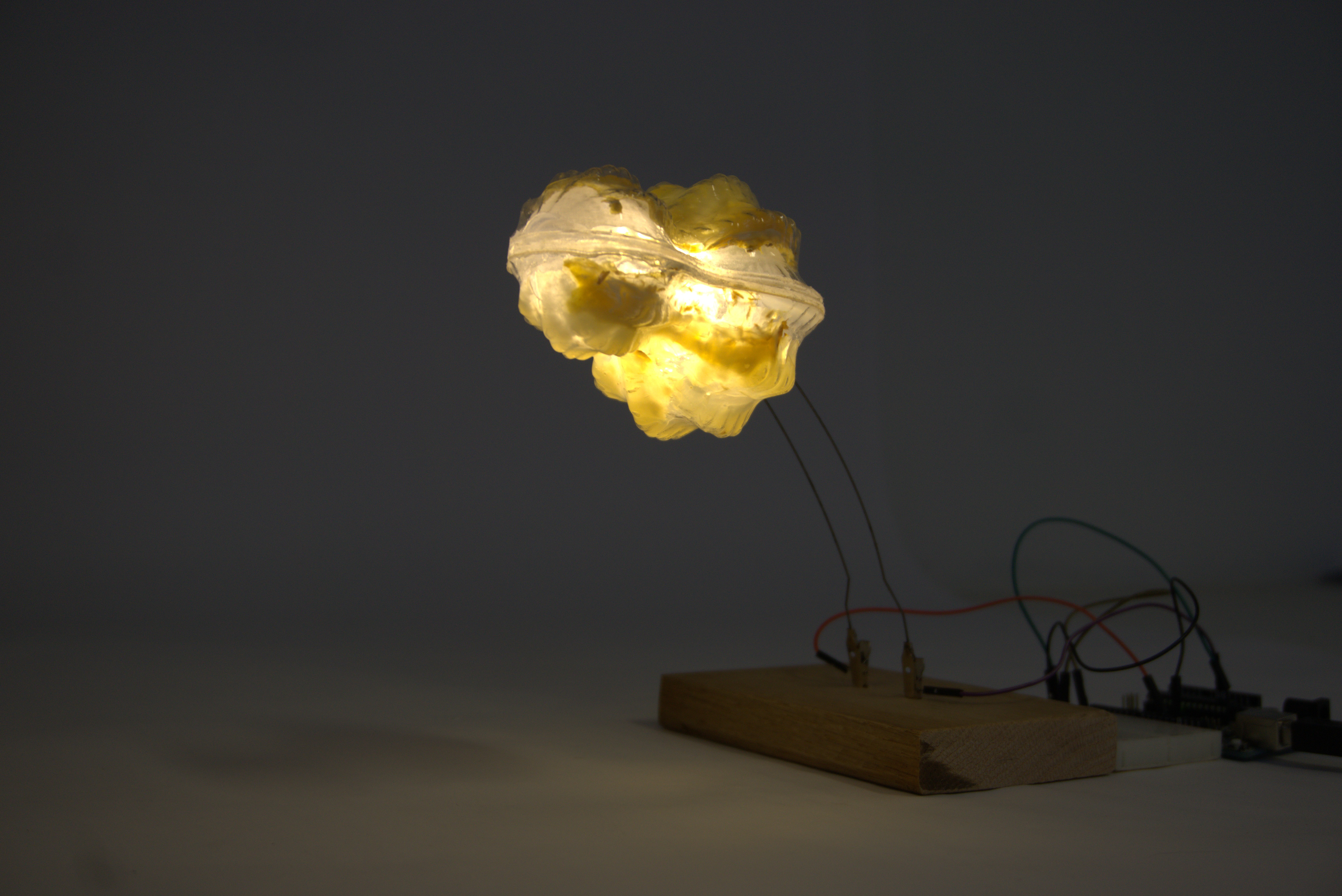
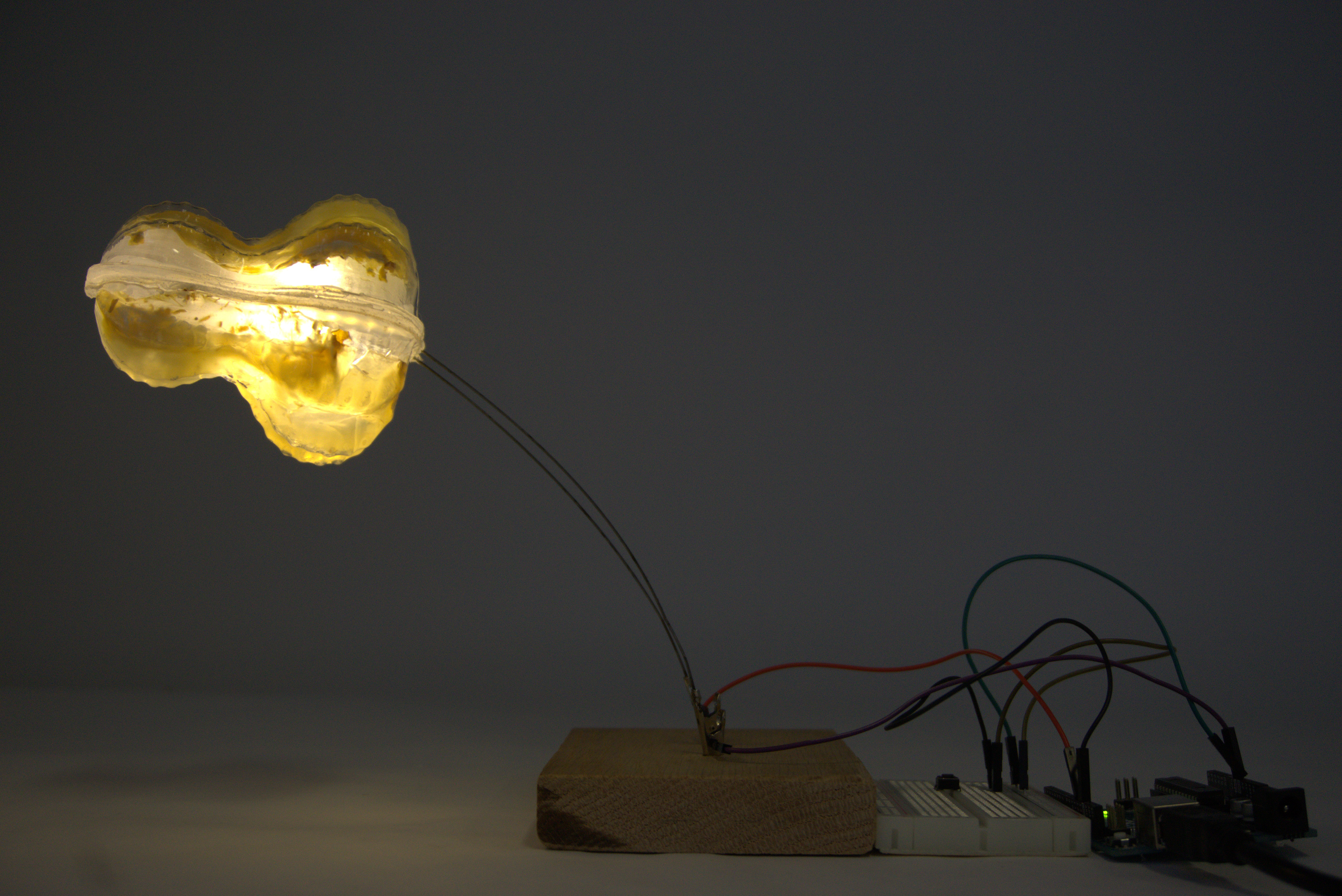
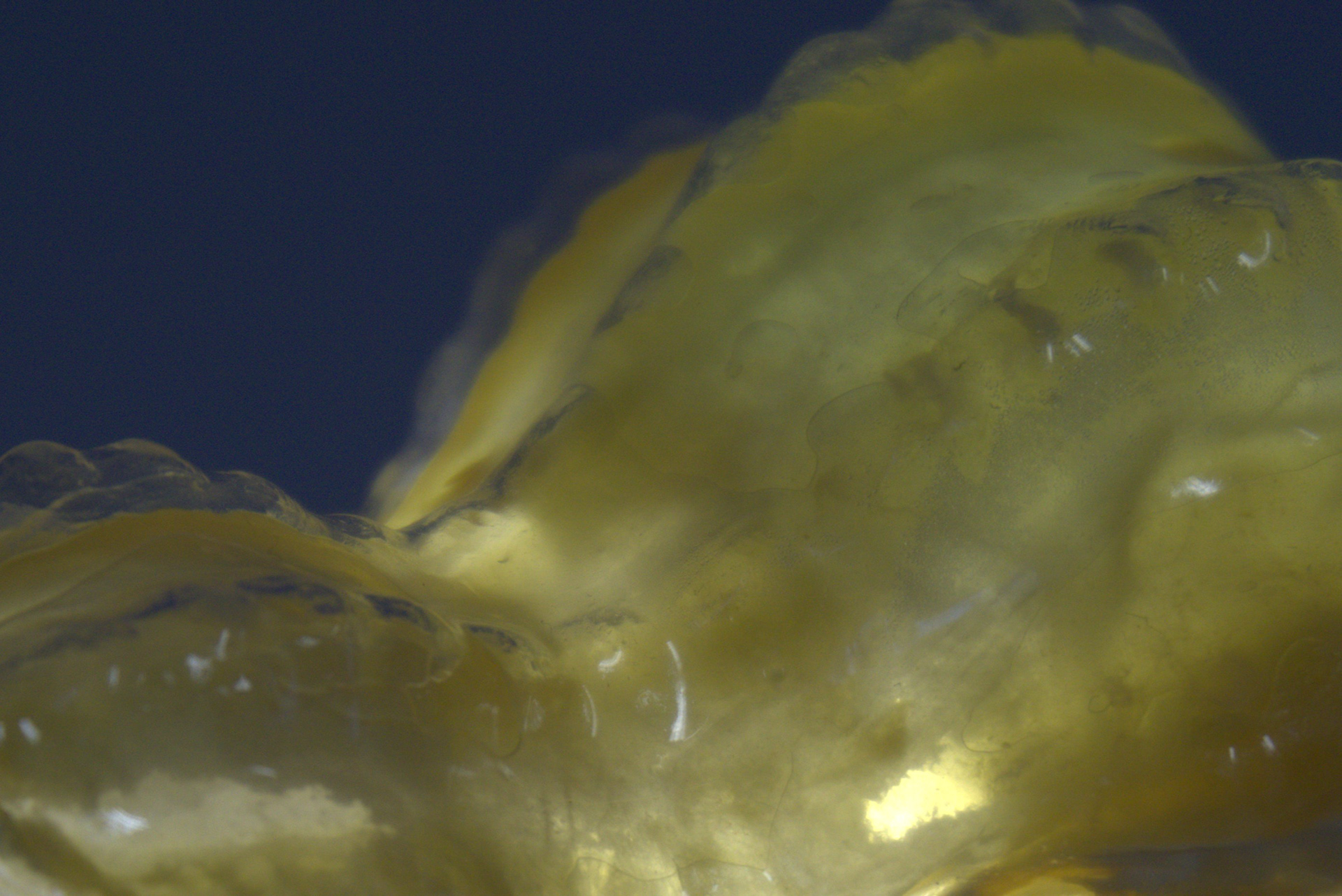
Machine: Vaccum Forming, 3D Printer
Material: PETG, Oyster Mycelium, Agar